Setting up an Emergency Action Plan
Setting up an Emergency Action Plan
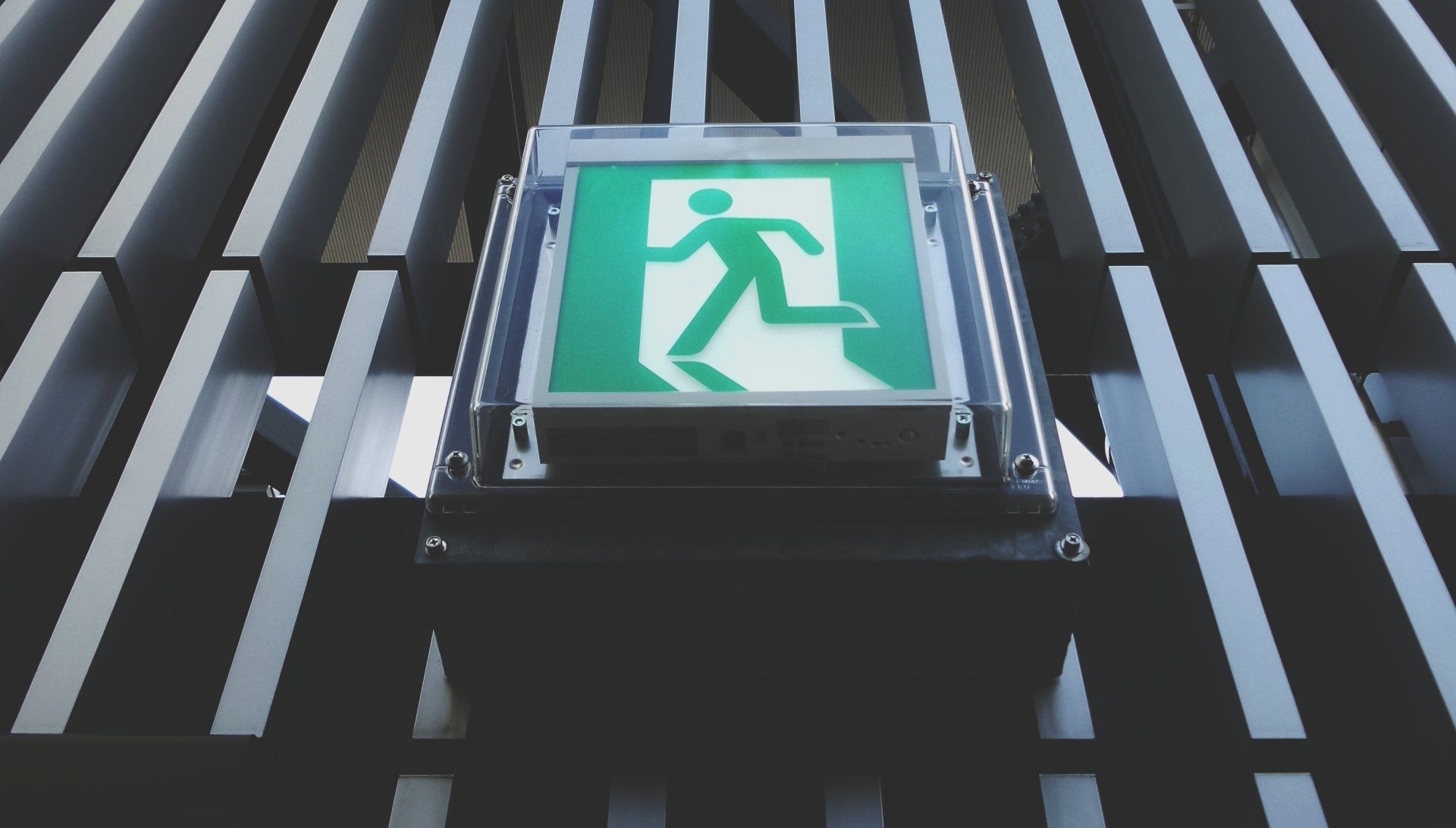
What is an Emergency Action Plan?
Your Emergency Action Plan is your source of all truth when it comes to how to prevent and react to hazards in your workplace. In any situation which may require an employee to do something in response to an incident in the workplace, you should have a clear outline or definition of what that response will be. The EAP is the documentation of this information.
Preparing an Emergency Action Plan (EAP) can seem difficult, even daunting. There are so many components, and it may seem like you couldn't possibly account for everything. Realistically there are a few key elements that make up an EAP, and by focusing on these concepts, you are more likely to capture all the hazards of your workplace, keep an organized safety system, and most importantly, be prepared to keep everyone safe.
Identifying Hazards
You have to start by identifying the components that you want to include. Some of these items may be compliant focused, while others will be specific to what you do in your company. The Occupational Safety and Health Administration (OSHA) has a full standard on what must be included, but then it is up to you to choose what depth you go into.
For instance, OSHA requires procedures for reporting a fire or other emergencies. You are in charge of determining what the other emergencies may be, and how to respond to them. Take the time to review your company procedures and identify where things could go wrong. Interview department managers and frontline workers to see what hazards they are facing on a day-to-day basis and if it is documented what to do in case something goes wrong. Are you a woodworking shop? Incorporate hazards for small particle accumulation. Are you an accounting office? Include specifics on screen fatigue and ergonomics.
The more you identify, the more you can encompass in your plan.
Organizing your Emergency Action Plan
Your EAP should act as the overarching document of all things safety. Wherever there is a doubt on what the rule is for anything safety, it should always go back to the EAP. A common mistake is that your EAP should be the manual for any and all situations. In reality, your EAP should act as the reference glossary for every procedure you have. Think of your EAP as a search engine result. You go through it to find what procedures are defined for your facility, and possibly a summary of the key points for that procedure. But you have to read the actual procedure, much like clicking on the link from your search, to read all the information around a situation.
The only procedures that should be included in your EAP are ones that are applicable to all of your other procedures.
Below are some examples of how to include some basic concepts.
Item | Include Details | Reference Documents |
---|---|---|
Evacuation Routes | X | |
Fire Prevention Plan | X | |
Air Quality Plan | X | |
Emergency Contact Information | X | |
Internal Communication | X |
Notice how more specific information is referenced, while the information that may apply to more than one reference document stays included in the Emergency Action Plan. No matter what the emergency is, you will most likely be exiting the building with the same strategy, hence the reason for keeping this procedure in the overarching document. However, your Fire Prevention Plan may change as new equipment is installed and/or removed. So rather than updating your Emergency Action Plan every time you get a new piece of machinery, you can update just the smaller portions of your safety system.
In addition, as training is executed towards your safety system, you begin to set up an easy-to-follow matrix that can follow your EAP. To follow our earlier example, all employees will need to be trained on items described in the EAP, but more specific procedures may only affect certain employees.
Training Item/Position | Warehouse Manager | Maintenance Technician | Operations Manager |
---|---|---|---|
Evacuations | X | X | X |
Fire Prevention Plan | X | X | X |
Fire Extinguisher Inspections | X | ||
Evacuation Headcount Procedure | X | X | |
Air Quality Monitoring | X | X |
Why the Emergency Action Plan is important.
Your Emergency Action Plan is the foundation of your safety system. Without it, you will not have a clear definition of hazards in your workplace, or general response tactics. Creating an EAP may not seem like the most exciting task. It may even seem time consuming and difficult. But creating a strong, organized EAP creates a strong base for a safety system to keep your company safe and in compliance.