Why PPE isn't always the answer
Why PPE isn't always the answer
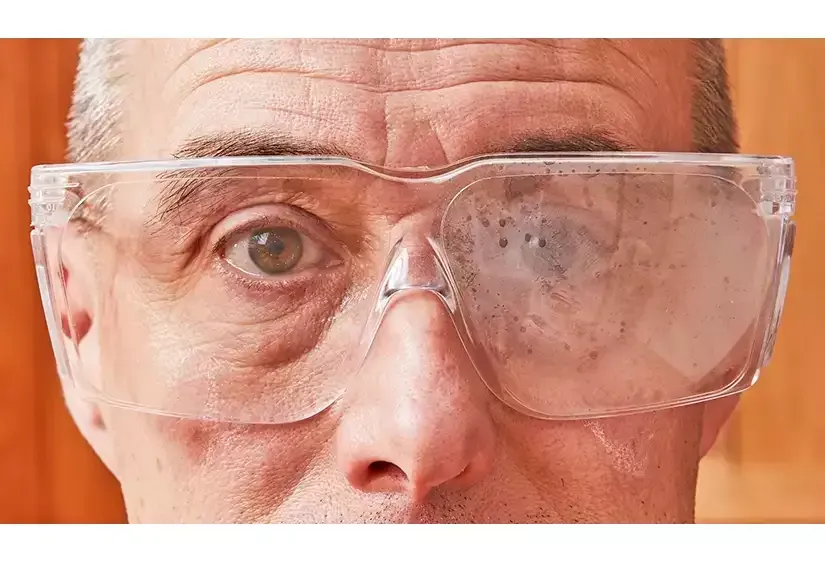
Have you ever had this thought?
Why are there no safety glasses at the PPE station when I just filled it earlier this week? Where are all the nitrile gloves and why does it seem like we are always out of the ones that fit me? Don’t my coworkers understand that if they don’t wear PPE, they are going to get hurt?
While Personal Protective Equipment (PPE) is easy to declare as the catch-all solution to keeping employees safe, it is the least effective form of protection from hazards, and possibly the costliest. While implementing a PPE policy may save time initially, you will quickly learn that a combination of your time, safe environment, and money will begin to dwindle.
Thinking about a typical manufacturing space, a general requirement is to have eye protection to enter, so they will put PPE stations at all entrances to ensure compliance. The thought is that this always promotes the idea of safety and eliminates one of the costliest violations to the employer if found responsible for injury. But let’s look at why this will cost companies more cost and resources.
PPE Stations
Prepare to find PPE everywhere except where you want it to be, on your employees and in the PPE stations. Anyone that grabs a pair of glasses will view them as a disposable resource and you will start seeing them in breakrooms, on machines, and even in people’s cars. Setting up a PPE station is a flashy way to promote safety, but weekly fill ups will start to wear you down and it will chew away your budget. There are three big cons to PPE stations.
THE RESPONSIBILITY
When you set up a PPE station, you take the responsibility of wearing PPE off the employee and put it on the employer. While it is our responsibility as safety professionals to make sure that our employees have access to the right equipment and use it, we are now adding the extra responsibility on ourselves to tell people weekly whether safety is going to matter. When your employee walks in Monday morning to see the PPE station empty, you are telling them that safety isn’t a priority that week. Management had more important things to do than to keep people safe, so production also must take priority over safety.
THE COST
Refilling cost money and time. Time also has a dollar amount associated with it, so refilling PPE stations cost money and more money.
Material: Refilling a PPE station weekly is going to cost roughly 30 dollars. Assuming two different entrance points you are looking at 240 dollars a month.
Time: 30 minutes a week is now lost to inspecting and refilling stations. That means you are losing 30 minutes of production from an employee. Considering half an hour of pay plus the lost production time turned into cost, let us assume that equates to another 35 dollars (depending on salary and widgets being produced) per month.
Material + Time = The Cost
Keeping PPE stations alive, assuming your process is flawless, is going to be around 3,300 dollars and 24 hours of work per year until you have retired that station.
THE HAZARD IS STILL THERE
By requiring PPE, you have waved the white flag. You have come to terms with the fact that a hazard that is so common that everyone is exposed to it and needs protection, has not been eliminated. You begin to build the workplace culture of “hazards are everywhere and just get used to it.”
So now what?
PPE has its place in the workplace, just as does every other control method. PPE is a great control method for non-routine tasks and can be very helpful in controlling hazards in an emergency. For routine tasks, you are better off using a control that may take more time and resources on the planning and implementation side, but will pay off in the long run for cost and time savings. Here is the best question.
WHAT IS THE HAZARD?
Ask yourself, what is the hazard? Why are we requiring employees to wear glasses? If you can’t think of anything, remove the PPE station. Your CFO will thank you; your production workers will thank you. You can also go to bed knowing you are not exposing someone to a hazard.
If there really is a hazard, how can you remove it? Great alternatives to PPE can include:
- Machine guards
- Change of process
- Removal of process
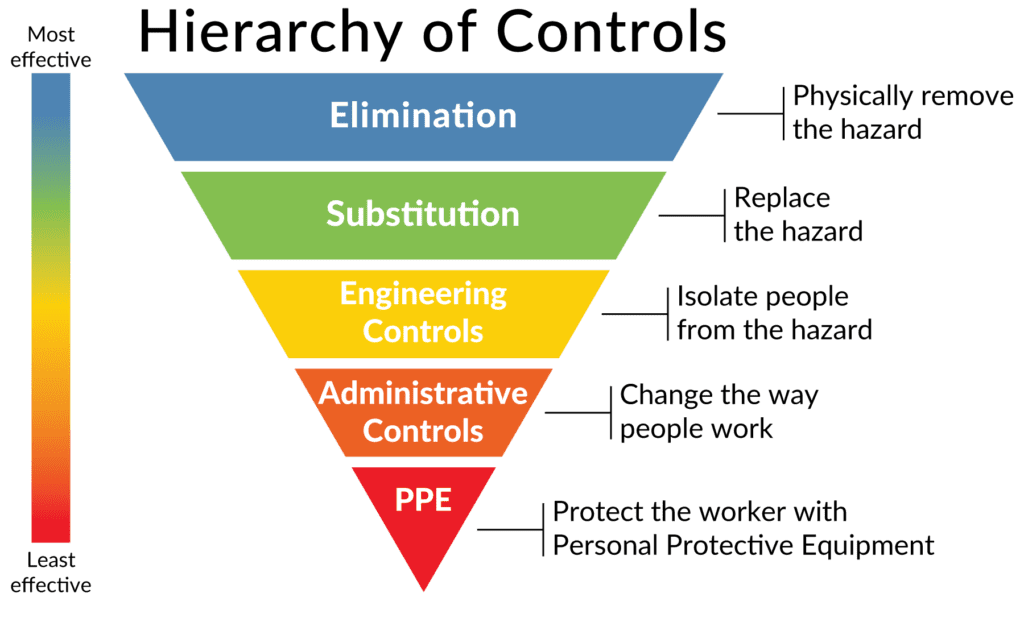
Sure, it can be easy to require safety glasses, and easy to push employees to follow these PPE policies, but what about gloves? What about respirators? By requiring bulky PPE, you can increase likelihood of non-conforming parts, accidents, and injuries. Prioritize the environment of your employees. Your coworkers and budget will be thankful.